The aerospace industry is inseparable from the injection molding industry.
Let’s take aircraft interior plastic applications-flame retardancy for example:
Taking into consideration the internal application of each aircraft, the internal materials must meet a variety of technical requirements to reduce the consequences of a fire in the cabin and ensure the safety of passengers.
In order to ensure the fire protection of aircrafts, the Federal Aviation Administration (FFA) regulates various fire test procedures (such as FAR 25.853) to prove that aircraft materials can meet specific performance standards when exposed to heat or flame.
Generally speaking, high-performance engineering plastics such as PEEK, PEI, and PPS can meet the flame retardant requirements without modification.
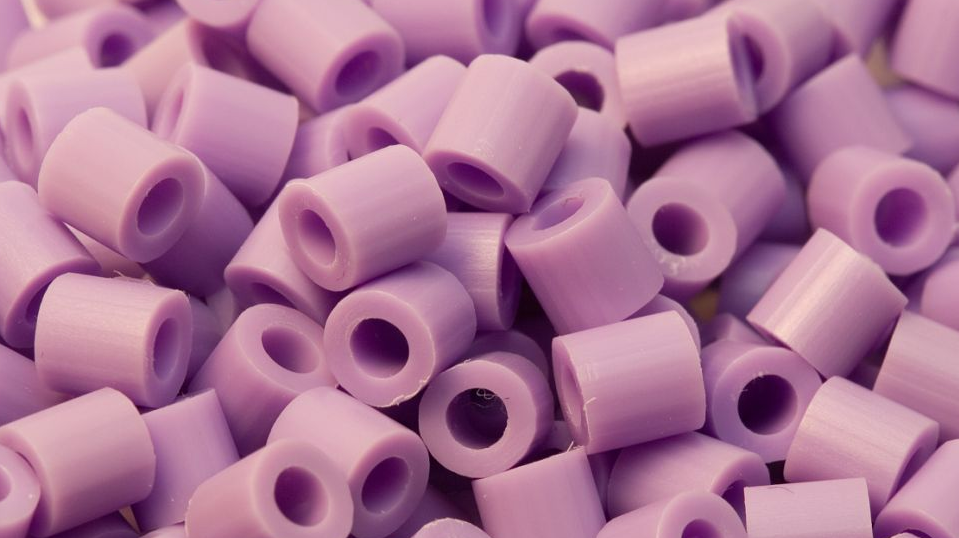
Stress
When choosing aerospace plastics, specific strength is also a key indicator of high mechanical properties. It determines the tensile strength of the material relative to density and shows the ratio of strength to weight.
When plastic parts are subjected to stress in applications, their mechanical properties play a particularly important role. The basic mechanical properties of plastics include:
◆Strength: a measure of the material’s resistance to external stress
◆Rigidity: a measure of the ability of a material to resist deformation
◆Hardness: a measure of the ability of a material to resist deformation under concentrated compressive loads
◆Toughness: a measure of the ability of a material to absorb energy during an impact
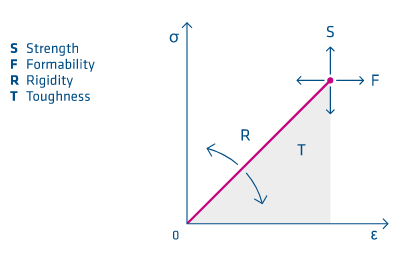
External plastic applications of aerospace components -UV Radiation Resistance:
Plastics used in outdoor applications are affected by weather conditions. Specific parts such as aircraft covers or satellite components usually require plastic materials that are weather-resistant and can withstand ultraviolet radiation, otherwise ultraviolet radiation will affect the appearance and mechanical properties of the plastic.
The black coloration of plastic is an effective way to protect it from the weather. Based on different application areas, plastics may be exposed to different types of radiation, so radiation-resistant plastics need to be used in the “exterior facing” parts of aerospace products. In addition, fluoroplastics such as PTFE and PVDF also have excellent UV stability in their natural state.
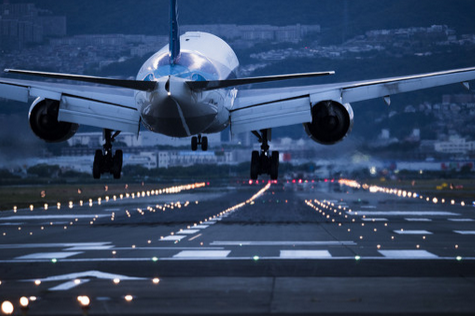
Aircraft internal circuit application-insulation
With their excellent electronic properties, engineering plastics cover the entire span from insulation, anti-static to fully conductive, which makes them an important choice for the electronics industry.
Pure plastic material has inherent electrical insulation. They have high resistance and can fully withstand current flow. Therefore, it is widely used in various applications, especially in the aviation field.
It is necessary to prevent the material from conducting electricity and causing harm to people and property. Typical applications include aircraft internal switches, overhead lights, aircraft internal wires and circuit boards, but also conductive, high temperature resistance features such as low air permeability!
Conductivity: The dissipation of static charge is essential for aerospace applications where highly sensitive electronic components are present.
High temperature resistance: Many aerospace plastic applications require materials to be resistant to high heat and have good aging resistance.
Low gas permeability: When selecting materials in aerospace applications that are exposed to vacuum, the gas permeability characteristics of the material are very important.
Injection Molding in the Field of Aerospace
For the aerospace industry, there are a variety of injection molded aerospace products.

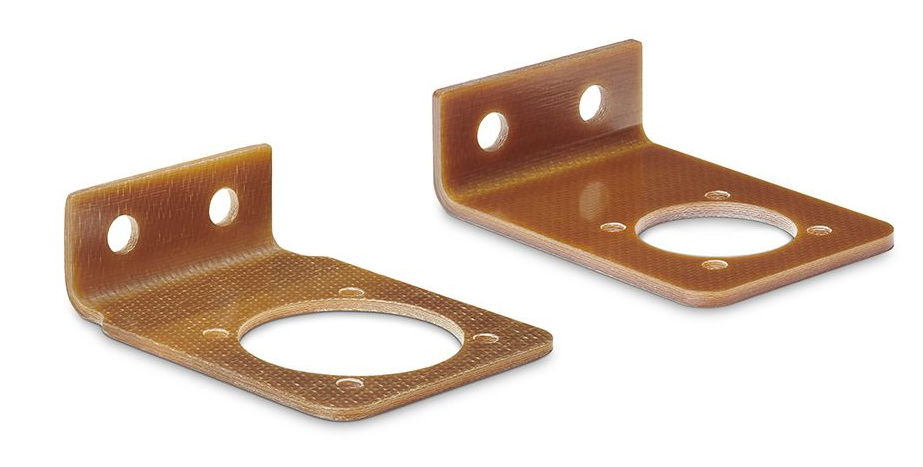
This is a lightweight product for aircraft interiors. It is a series of production parts based on composite plastic materials; lightweight and high-strength plastic materials have become one of the indispensable materials in high-end applications in the aviation field.
For passenger aircraft, weight per kilo is important, which is why metal is increasingly being replaced by plastic solutions, as is the design of aircraft interiors. In particular, thermoplastic composite materials provide significant weight reduction for aircraft supporting companies without the need to compromise on mechanical properties.
Injection molding: light but extremely high-performance lubrication plug
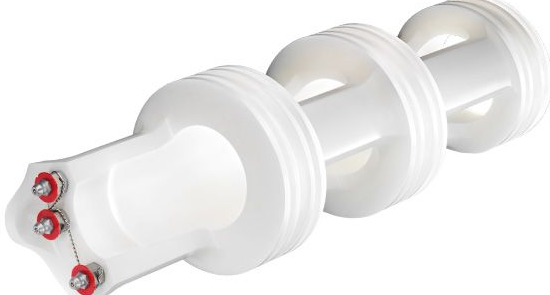
Image/photo by ensingerplastics
In the aerospace industry, high-performance plastics used in every component need to meet very stringent requirements. The lubrication plug of the landing gear needs to use plastic materials that are dimensionally stable, have good grease resistance, and are environmentally friendly.
Due to the working temperature and fire safety requirements, low-cost materials are not adequate. In order to meet the aircraft performance requirements, some parts such as lubricating plugs molded by injection molding are lighter than the aluminum used before, but have extremely high performance.
Electric Brake System
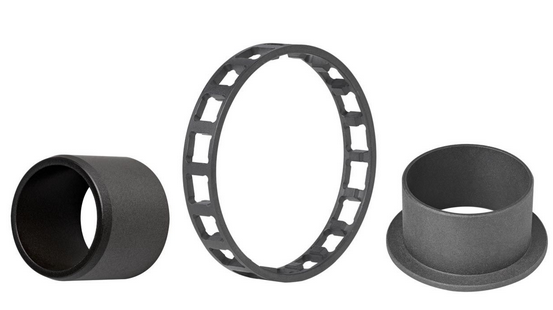
The design of modern passenger aircraft requires the development and introduction of new technologies such as “all-electric braking systems”. Consider using an electric braking system to reduce maintenance and improve reliability. Responding to the engineering challenges of manufacturing these new systems requires radical changes in design thinking and materials used. Electric braking will become the industry standard for all new commercial aircraft.
In the electric brake system, the parts produced include bearing rings, thrust rings, thrust washers and toroidal bearings. The products produced need to have higher wear resistance and load-bearing properties, as well as higher reliability.
SPARK – Spark Series All electric
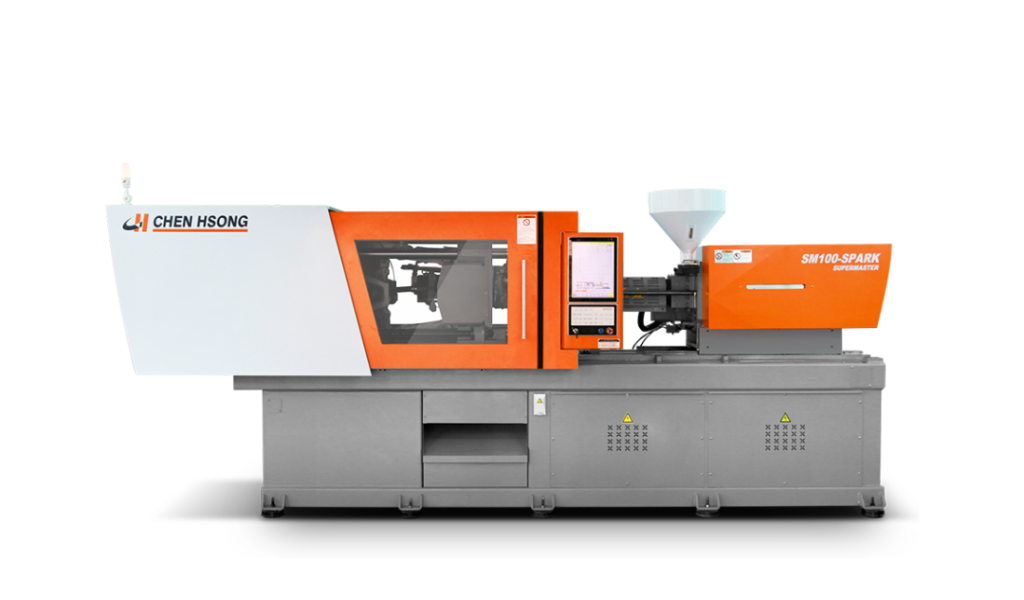
SPARK series can produce some complex parts in the aerospace industry and can meet the requirements of precise tolerances and surface finish. Even for the production of high-demand precision parts and complete components, SPARK all-electric motors can also meet the requirements, such as insert molding and overmolding and multi-component injection molding.
The stable, accurate and fast SPARK series injection molding machine will be used increasingly in the field of aerospace injection molding.